Whether you have 100 SKUs or 10,000, inventory management is a complex subject that is key to a company’s financial health.
You need to be able to respond to constantly changing demand while optimizing the total cost of your stock.
In the context of the last three years marked by the pandemic, shortages of certain raw materials, and congested commercial ports, choosing the right inventory management method is essential.
Today, we will compare two main methods: the Min/Max method and the Safety Stock method.
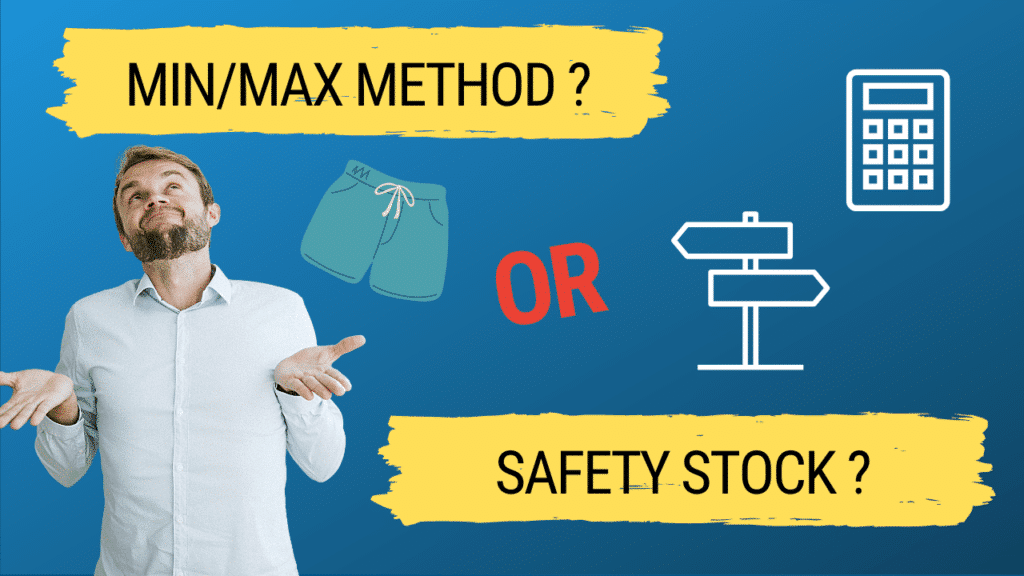
Example
To illustrate our comparison, let’s take the example of a company selling shorts:
- Average sales (AS): 150 quantities/week
- Delivery time: 3 days
- Security time: 1 day (to be chosen according to the reliability of delivery times and/or the proximity of your suppliers)
Definitions
Before we get started, here are a few terms to redefine so that we’re on the same wavelength…
- Safety stock: Safety stock (SS) is a buffer stock that cushions stock reductions due to peaks in demand and/or unforeseen supply delays. Safety stock can be calculated as follows: SS = AS x safety lead time. In our example, the safety stock is 150 quantities.
- Reorder points: reorder points represent the points at which you need to order the correct quantity. Reorder points can be set at regular intervals (beginning of each month, beginning of each week, etc.) or according to your stock levels (minimum stock, maximum stock).
Here, order points (in red) are set at regular intervals. When stock is at its lowest, you order until you reach maximum stock.
This method is still effective when your forecasts are reliable, or you can be delivered the same day.
But as soon as average sales fluctuate or delivery times lengthen, you find yourself out of stock… How can you avoid this scenario?
➡️ by moving your order bridges according to your stock levels, in combination with a safety stock :
🧮 Formula: RP (reorder point) = SS (safety stock) + AS (average sales) x Total lead time*
*Total lead time: Order lead time + Delivery lead time
Let’s go back to our example: RP = 150 + (150 x 3) = 600 qts
You will therefore place an order when your stock level reaches 600.
Min/Max method
The Min/Max method is based on a simple principle of determining minimum and maximum stock levels.
Minimum level (MIN): The minimum order point is calculated by multiplying the average sale (VM) by the sum of the delivery lead time (and possibly a “safety lead time”). This formula is used to determine when an order must be placed to avoid stock s
🧮 Formula: MIN = AS x (lead time + safety lead time)
Maximum level (MAX): The quantity to be ordered to reach the maximum stock level is calculated by multiplying the average sale (VM) by a fixed ratio, usually between 1.5 and 2.5. This formula ensures that stock does not exceed an optimum level, thus avoiding overstocking.
🧮 Formula: MAX = AS x Fixed ratio
This method takes into account both average sales and delivery times. Thus, as average sales increase, so do minimum and maximum reorder points. Similarly, when delivery times are longer, the minimum level is more important to cope with unforeseen events.
🖊️ Let’s take our example again: average sales (AS) are 150 quantities per week, delivery time is 3 days, and safety time is 1 day.
Calculation:
↘️ MIN = 150 x (3 + 1) = 600 quantities
️ ↗️ MAX = 600 x 1.5 = 900 quantities
➡️ Safety Stock (SS) = 150 quantities
So, according to this method, you should place an order when your stock reaches 600 quantities and keep the maximum stock at 900 quantities. The “safety stock” of 150 quantities helps cushion demand or lead times variations.
You can add adjustments to the Mini Maxi stock method to go even further. For example:
A seasonality coefficient ☀️: If your products are subject to seasonal variations (seasons, back-to-school, vacations, etc.), you can add a seasonality coefficient to your minimum reorder point. This allows you to adapt stock levels to seasonal fluctuations.
🧮 Formula: MIN = AS x (lead time + safety lead time) + Seasonality
A service rate coefficient 🤝 : Instead of using a fixed ratio, you can replace it with the service rate coefficient (Z) calculated from the normal distribution law. This approach allows you to consider demand variability and adjust stock levels accordingly.
🧮 Formula: MAX = AS x service rate coef Z
Safety Stock + Order Point Method
In addition to average sales and lead time, other parameters can be considered to determine safety stock more precisely. Another commonly used formula is as follows:
🧮 Formula: Safety stock (SS) = Z x Standard deviation of demand x Root (average lead time)
In this formula, Z represents the service rate, which can be calculated according to certain criteria. The standard deviation of demand measures the dispersion of sales in relation to the average.
🖊️ Example: Let’s assume that Z equals 2.05 and that the standard deviation of demand is 30 quantities, with an average lead time of 3 days.
Calculation: Safety Stock (SS) = 2.05 x 30 x root(3) = 106 quantities
Combining this method with the economic quantity (EQ) or Wilson’s formula, which takes into account lead times (LT), order costs (OC) and stock costs (SC), you can determine the reorder point (RP):
🧮 Formula: Economic Quantity (EQ) = Root of (2 x LT x OC / SC)
This method is more complex, involving several parameters in the calculations. I recommend using it when your stock management presents many uncertainties and high stock levels.
Method comparison
The Min/Max method
You can order later than the second method with the Min/Max method.
It’s very easy to set up and suitable for short replenishment lead times. The uncertainty of lead times and demand can be covered by an arbitrary “safety time”. If your lead times are short and your replenishment frequency is high, you don’t need this safety time.
This method does not consider the economic order quantity (EOQ), including ordering and inventory costs.
Safety Stock + Reorder Point + Economic Quantity
With the safety stock method combined with reorder point and economic quantity, the total cost of your stock will be better optimized and uncertainty better covered.
It is best suited to long lead times and large volumes.
Conclusion
You must adapt and find the right inventory management method depending on the situation. If your stock levels are low, your lead times are short (less than a few days), your suppliers are close to your warehouses or sales outlets, and your demands are predictable or stable, we recommend the Mini Maxi method.
On the other hand, if your volumes are high, lead times are long, your suppliers are on the other side of the world, and demand is highly volatile, we recommend the safety stock method combined with reorder point and economic quantity.
In all cases, it’s important to implement automated systems to facilitate inventory management. The ABC XYZ method, for example, can help you optimize your inventory management process. Automation will enable you to be more efficient and reduce errors.
More content on inventory management
I also recommend that you consult our video tutorials:
- Safety Stock Formula & Calculation: The 6 best methods (Excel Tutorial)
- EOQ formula for optimizing order quantities (Excel Tutorial)
- 11 solutions to optimize your Inventory
Become an Inventory Management Expert
If you want to go to the next level, join my 7-day workshop (free): How to reduce stockouts and overstocks.
7 days of free advice to optimize your inventory from scratch:
👉 Gain visibility into your inventory and service levels.
👉 Simplify, automate your inventory management
👉 Improve your performance and regain control of your time.